When it comes to selecting the right clamp for your needs, there are many factors to consider.We have many customers who frequently ask us various questions about different types of clamps, such as the differences in styles, usage scenarios, size ranges, and installation methods. Today, we will discuss a few common questions:
Hose clamp in the installation need to pay attention to what problems?
1. The clamp shall be free from defects such as pores, sand holes, shrinkage cavities, and cracks.
2. The diameter of the pipe end should be selected with a positive deviation; otherwise, the clamp will not exert sufficient pressure on the sealing ring, affecting the sealing performance of the joint.
3. The material and performance of the sealing ring must meet the requirements. The sealing surface should be free from bubbles, impurities, cracks, and unevenness. Aging rubber rings should not be used.
4. Splattering and impurities during the welding of the pipe end and the retaining ring affect the sealing of the pipe end. The weld slag on the sealing surface should be cleaned before installation to ensure the sealing effect.
5. The theoretical movement distance of the retaining ring within the clamp should be half of the joint's expansion and contraction amount, and it should be measured and verified. If it does not meet the requirement, it will not satisfy the pipeline's expansion and contraction needs. To ensure the sealing effect, the matching left and right pipe ends with the clamp should be used before delivery. In actual projects, ordinary pipes should not directly replace pipe ends. Additionally, there are requirements for the perpendicularity of the pipe end face to the axis and the flatness of the end face itself. If the dimensions are not standard, the expansion and contraction of the joint will be significantly reduced, failing to meet the usage requirements.
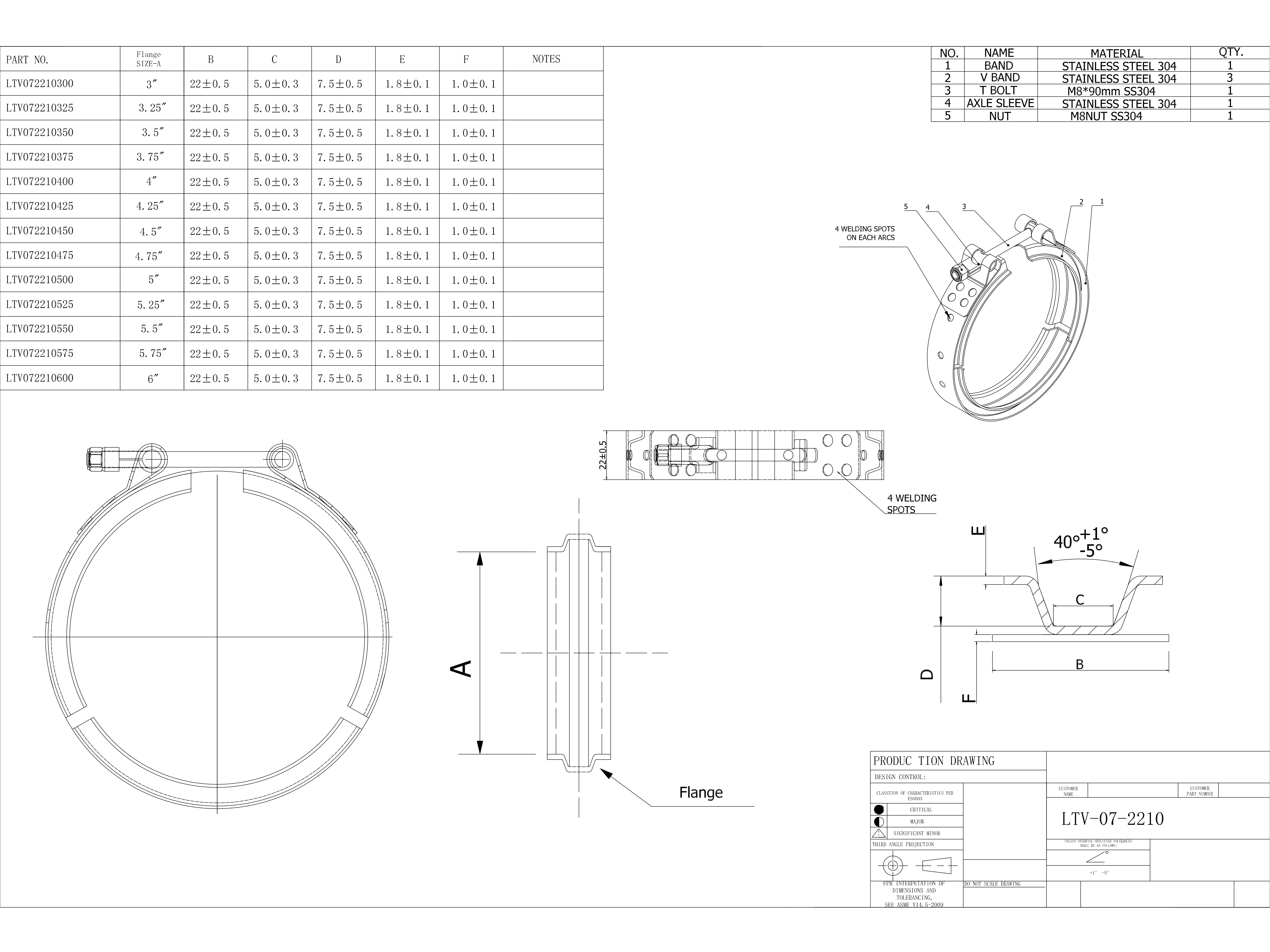
What is the difference between a diameter clamp and a variable diameter clamp?
The conventional sizes for Butt joint clamps range from 2 inches to 8 inches; the conventional sizes for Lap joint clamps range from 1.5 inches to 6 inches. The difference between Lap joint clamps and Butt joint clamps lies in the fact that Lap joint clamps have an additional convex-concave section in the middle of the steel strip. During the production of Lap joint clamps, we use a hydraulic press to form the steel strip into two different diameters. This allows our Lap joint clamps to be used on pipelines where a large pipe needs to be clamped to a smaller pipe. The design of varying diameters ensures that our product fits more snugly on the pipeline, providing better tightness, sealing, and an enhanced appearance.
How to define the size of our Lap joint clamps: Lap joint clamps consist of two diameters. The larger diameter part fits over the flared pipe, and the smaller diameter part fits over the regular pipe. The size of the smaller diameter is what we typically refer to as the size of the Lap joint clamp.
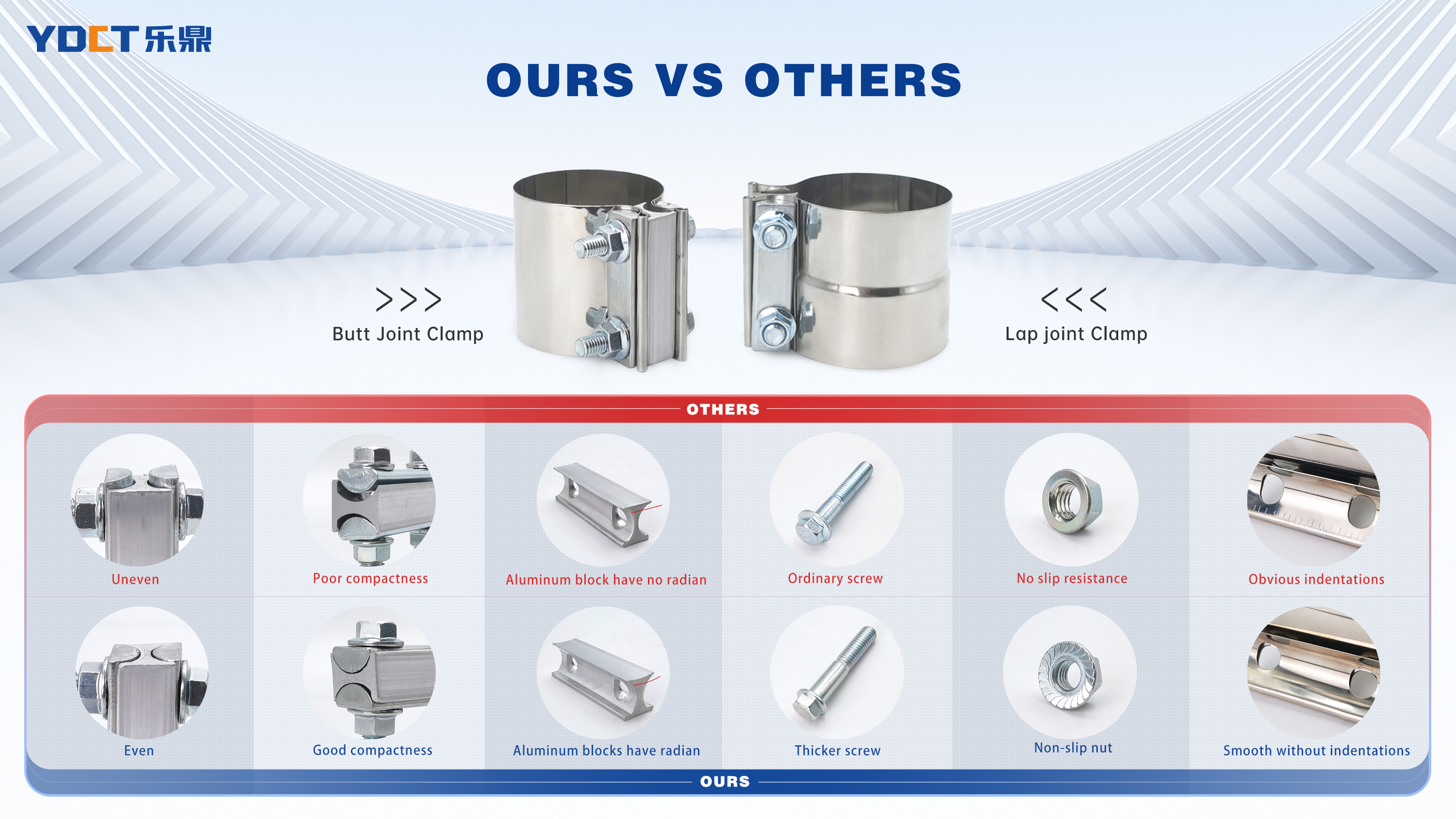
Spring clamp and mini clamp function difference, when to use them?
Features of Spring Clamps:
1. 360° Precision Design: The inner ring is designed with precision, forming a complete and uniform circle when sealed, enhancing the sealing performance.
2. Burr-Free Edges: The material is processed to have smooth edges, effectively preventing damage to the pipeline.
3. European Standard Surface Treatment: The surface treatment meets European standards, with salt spray tests exceeding 480 hours.
4. Easy Installation: Simple and convenient to install.
5. High-Strength Mechanical Performance: Continuous elasticity tests ensure high-strength mechanical performance.
Our standard export packaging uses cardboard boxes, with different quantities packed according to specifications and dimensions. Each box typically weighs no more than 15 kilograms. We can also provide sealed bag packaging.
Features of Mini Clamps:
Mini clamps are used for micro fuel lines, diesel or gasoline hose clamps, sealing hoses to prevent fluid leakage. The steel strip has a bandwidth of 9mm and a thickness of 0.6mm, with a slotted head screw. The recommended installation torque is 2.5Nm. The current supplier’s screw specifications are as follows: for screws ≤9-11mm, the screw size is M4*15mm, and for sizes up to 32-34mm, the screw size is M4*19mm. Different manufacturers may have varying screw lengths.
The reason they are called mini clamps is due to their small size, with the largest diameter being 34mm. This means the clamp can secure pipes with an outer diameter of up to 34mm. They are commonly made of galvanized iron or 304 stainless steel and are suitable for securing hoses, pipes, cables, fuel lines in household, automotive, industrial, and marine applications.
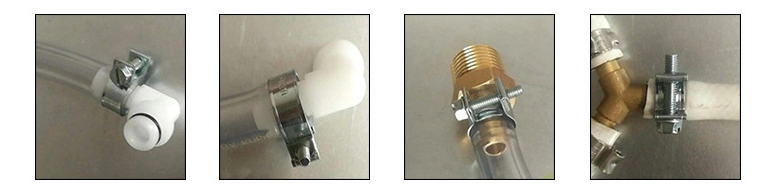
We know there are still many questions about clamps that we haven't covered. Stay tuned for more updates, and feel free to reach out with any specific queries you have about our clamps. We're here to help and provide you with the best solutions for your projects.